Maximizing Efficiency: Top Strategies for Selecting the Best Liquid Packaging Machine
In today's rapidly evolving manufacturing landscape, the selection of the right liquid packaging machine is crucial for maximizing operational efficiency and meeting consumer demands. According to a recent report by Grand View Research, the global liquid packaging market is projected to reach $500 billion by 2025, driven by the increasing demand for beverage and food products. As businesses strive to enhance productivity, reduce overhead costs, and maintain sustainability, identifying the best liquid packaging machine becomes paramount. Companies that invest in state-of-the-art packaging technologies can improve their throughput and reduce wastage, ultimately increasing their competitive edge. This blog will explore top strategies for selecting the most efficient liquid packaging machine, ensuring manufacturers are well-equipped to navigate the complexities of the packaging industry.
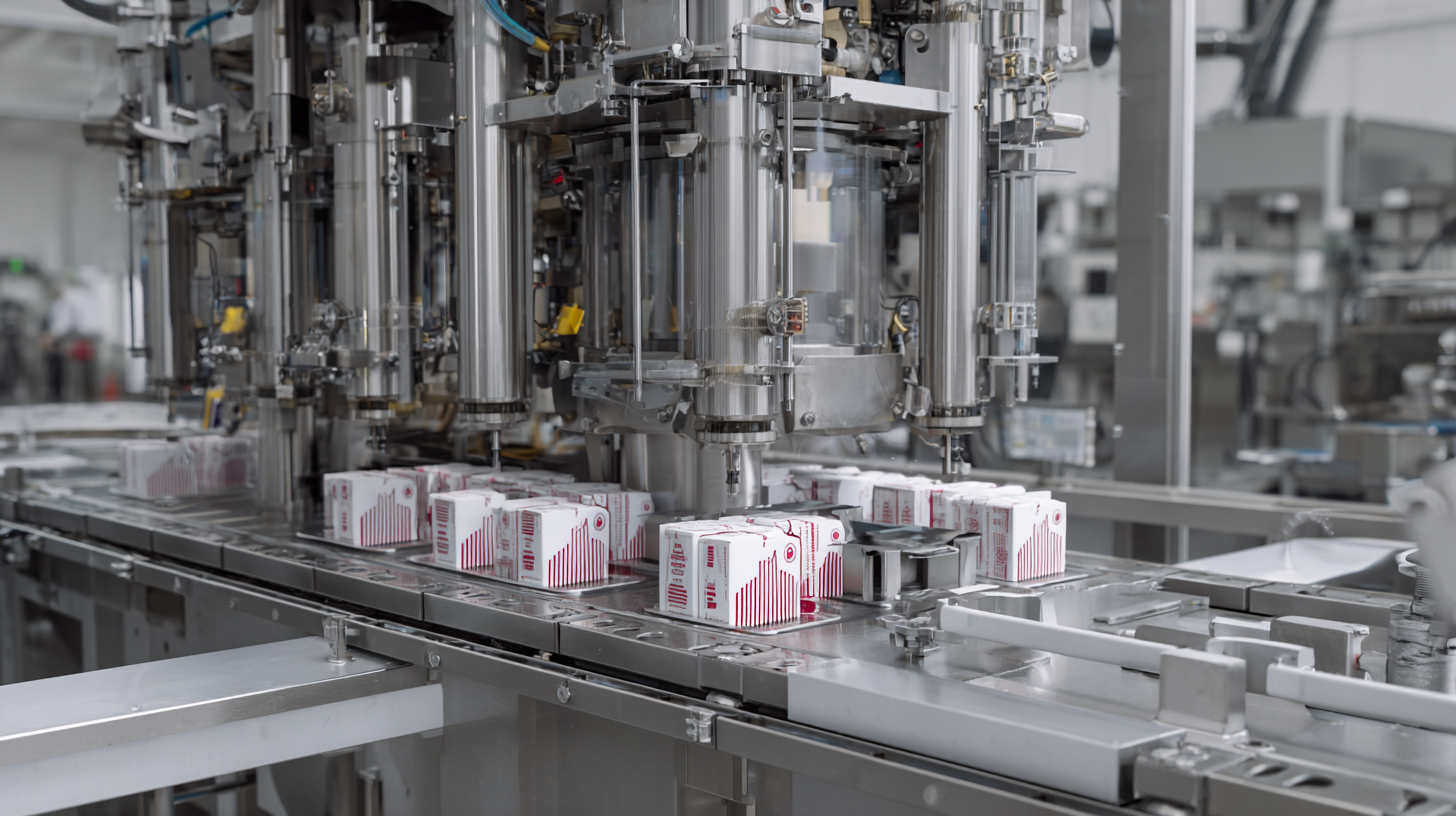
Understanding the Importance of Liquid Packaging Machine Certifications in Trade
When selecting a liquid packaging machine, understanding the importance of certifications cannot be overstated. Certifications ensure that the machinery complies with safety, quality, and environmental standards, which is crucial for maintaining product integrity. In today’s market, where sustainability is becoming increasingly prominent, certified machines often come with eco-friendly features that align with current consumer preferences. This focus not only meets regulatory requirements but can also enhance your brand's reputation.
Tips for Selecting Certified Machines:
- Verify certifications from recognized organizations to ensure compliance with industry standards.
- Look for machines that incorporate sustainable practices, such as using responsibly sourced materials. This can meet rising consumer demand for environmentally friendly products.
- Consider the long-term benefits of investing in certified technology, as it often translates to increased efficiency and reduced operational risks.
In the context of recent trends, such as a heightened emphasis on traceability and sustainability in sectors like pet food and beverages, opting for certified packaging solutions can give your business a competitive edge. As the industry evolves, making informed choices regarding liquid packaging machinery will be essential for success.
Evaluating Key Features in Liquid Packaging Machines for Maximum Efficiency
When selecting a liquid packaging machine, evaluating key features is paramount to maximizing efficiency in production. One of the critical factors to consider is the machine's speed and output capacity. Choosing a model that can handle high volumes without compromising quality will streamline operations, allowing for seamless integration into existing production lines. Additionally, machines with adjustable speed settings offer flexibility to accommodate various product types and fill levels, ensuring that you can adapt to changing demand quickly.
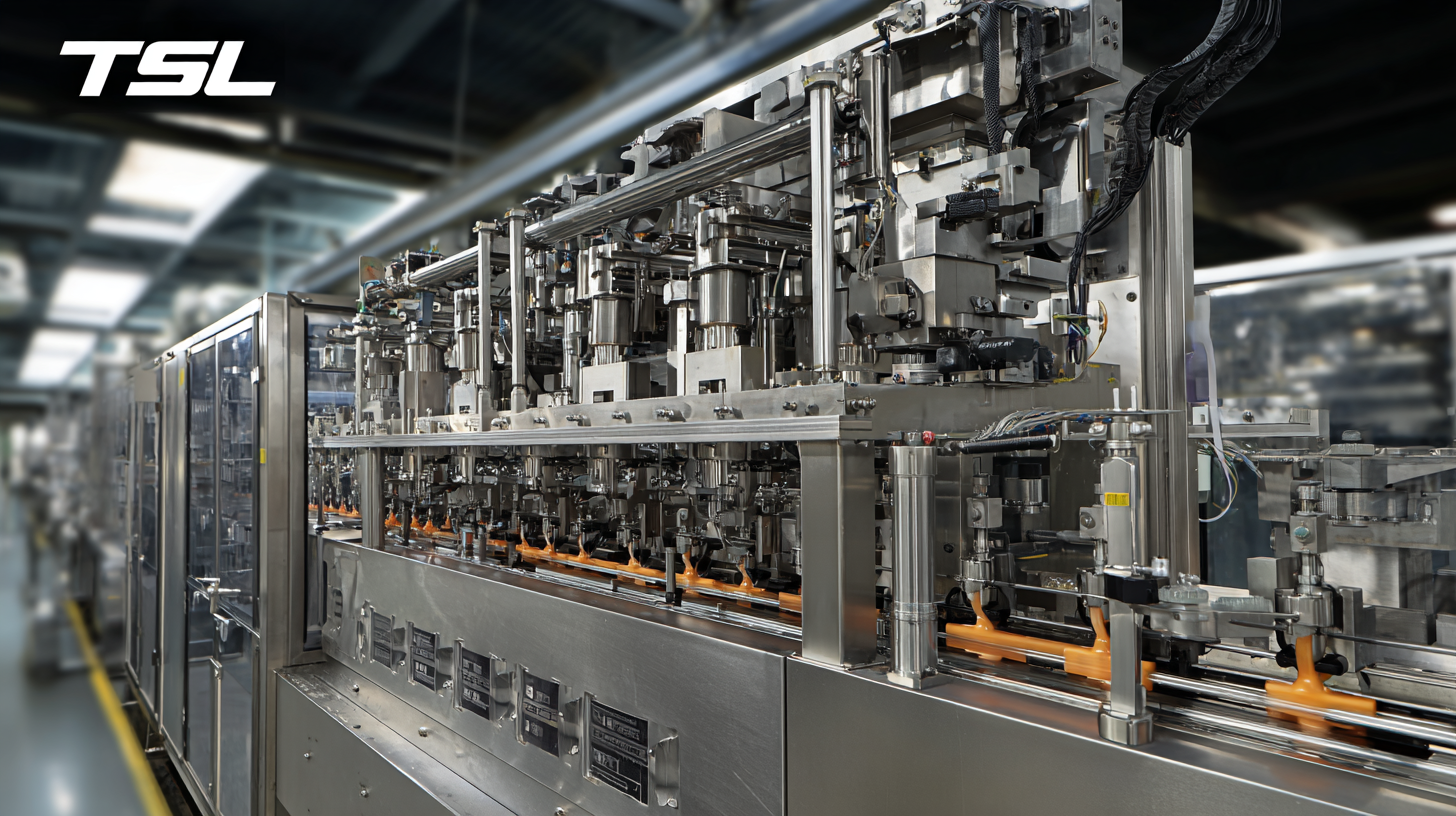
Another essential feature to look for is the machine's compatibility with different liquid types, including viscous, textured, or sensitive products. Advanced liquid packaging machines equipped with precision filling technologies minimize waste and enhance accuracy, which is particularly crucial for brands focused on sustainability and cost-effectiveness.
Furthermore, user-friendly controls and automation options can significantly reduce training time and operational errors, leading to a more efficient workforce. Prioritizing these key features will not only improve the performance of liquid packaging systems but also contribute to a more streamlined and cost-effective production process.
Comparative Analysis of Top Brands in Liquid Packaging Technology
When selecting the best liquid packaging machine, a comparative analysis of top brands in liquid packaging technology can significantly enhance decision-making. Understanding the market landscape, which includes advancements in liquid pouch packing and blow-fill-seal technologies, is crucial for businesses aiming to optimize their operations. Brands are innovating with features that increase efficiency, reduce waste, and cater to diverse product ranges—from cosmetic liquids to food-grade beverages.
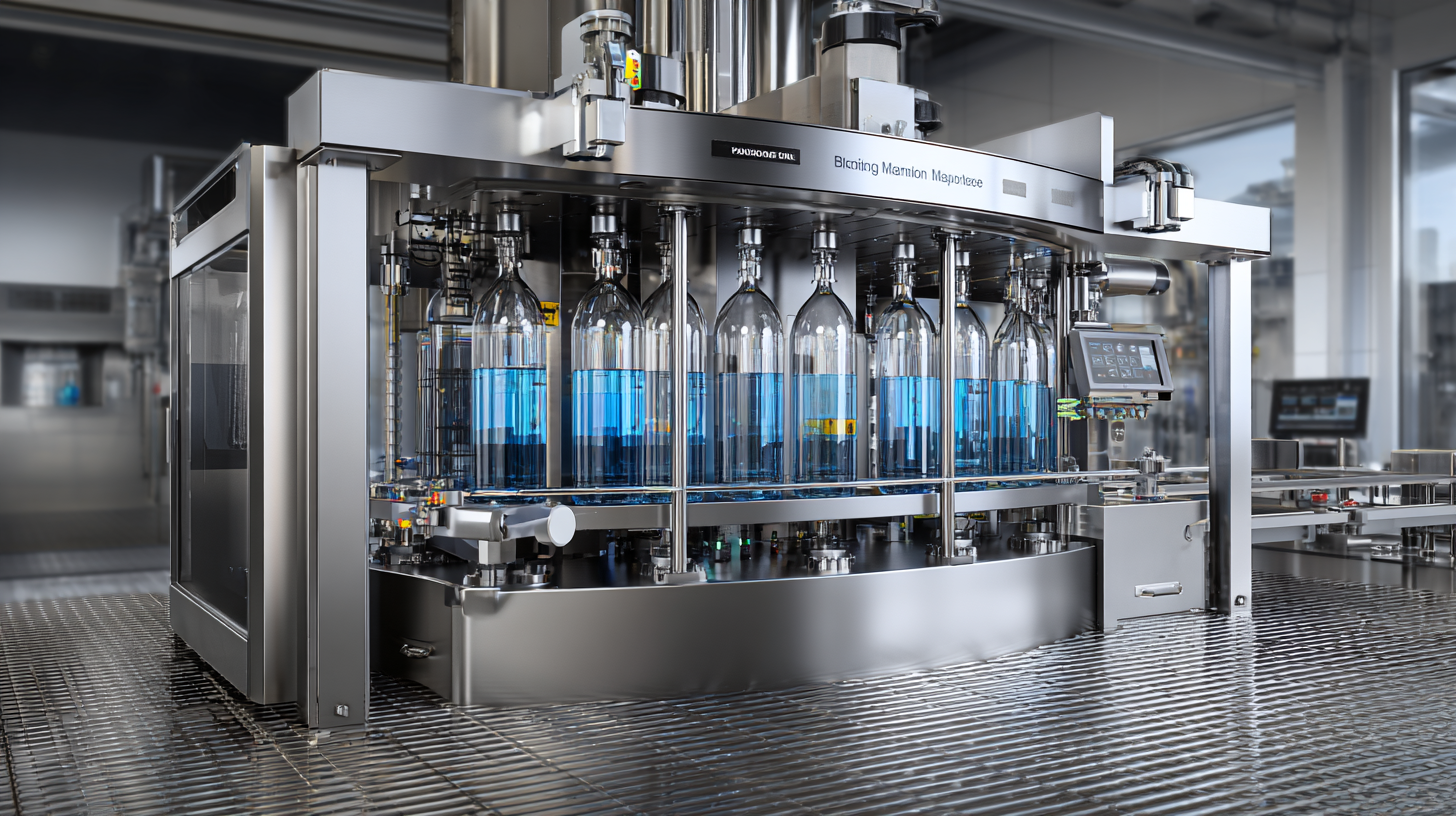
Additionally, the shift toward sustainability influences the choice of packaging solutions. The emergence of biodegradable materials and eco-friendly paper-based bottles reflects changing consumer preferences and regulatory demands. Brands that prioritize sustainable packaging not only align with environmental goals but also gain a competitive edge in a market increasingly focused on ecological responsibility.
Understanding how these factors interplay can aid manufacturers in choosing the most suitable liquid packaging machine tailored to their specific needs while staying current with industry trends.
Guidelines for Importing Liquid Packaging Machines: Regulatory Considerations
When it comes to importing liquid packaging machines, regulatory considerations play a crucial role in ensuring compliance and efficiency.
According to a report by Technavio, the global liquid packaging market is anticipated to grow by over $68 billion from 2020 to 2025, making it imperative for businesses to adhere to the necessary import regulations.
Various regions have their own set of compliance guidelines; for instance, the Food and Drug Administration (FDA) in the United States has stringent requirements for food and beverage packaging, which includes materials safety and labeling standards.
Understanding these regulations not only speeds up the import process but also enhances product safety and marketability.
Additionally, beyond safety and compliance, importers must consider the certification standards applicable to their liquid packaging machines.
The International Organization for Standardization (ISO) provides key certifications that can improve operational efficiency and reduce the likelihood of non-compliance penalties.
According to a report by MarketsandMarkets, companies with ISO-certified processes experience a 12% reduction in overall operational costs, showcasing the financial benefits of aligning with international standards.
Therefore, businesses must approach the importation of liquid packaging machines with a comprehensive understanding of regulatory guidelines, ensuring their processes are in line with industry best practices.
Best Practices for Maintaining Efficiency in Liquid Packaging Operations
Maintaining efficiency in liquid packaging operations is crucial as the market rapidly evolves. With the global liquid packaging equipment market expected to reach a staggering $8.2 billion in 2024, driven by increasing demand for packaged beverages, it’s imperative for companies to adopt best practices. A compound annual growth rate (CAGR) of over 5.8% from 2025 to 2034 emphasizes the urgent need for efficient machinery and processes to keep pace with industry growth.
One of the most effective strategies for maintaining efficiency is regular equipment maintenance. This includes routine inspections and timely repairs, which can prevent costly downtimes. Implementing energy-efficient machines not only reduces operational costs but also enhances production capabilities. Additionally, training staff on the latest technologies in liquid packaging can significantly minimize errors and boost productivity. As businesses navigate this growing market, focusing on these best practices will be key to optimizing their liquid packaging operations.